Laser Cladding Services
At Synergy Additive, the laser cladding process involves directing a high-powered laser beam onto a metallic substrate to create a precise melt pool. Concurrently, metallic powder or wire feedstock is introduced into this melt pool, melting and bonding metallurgically to the substrate as it cools. Laser Cladding typically involves adding only a few layers of the deposited material to dimensionally restore or enhance the surface characteristics of an existing component, in a process referred to as Surface Enhancement.
What Is Laser Cladding?
Laser cladding is an advanced additive manufacturing process that enhances or repairs the surface of a component by applying a high-powered laser to fuse a metallic coating onto a substrate.
This method improves wear resistance, corrosion protection, and overall performance by creating a metallurgically bonded layer with minimal dilution. Unlike traditional welding or thermal spray coatings, laser cladding delivers precision, reduced heat input, a metallurgically bonded layer that does not chip or peel and exhibit superior material properties.
Industries such as aerospace, energy, mining and heavy machinery rely on laser cladding to extend component life, reduce downtime, and optimize performance. Synergy leverages cutting-edge laser technology for high-quality, durable results.
How Does the Laser Cladding Process Work?
The Laser Cladding process uses a laser beam to form a melt pool on a metallic substrate. Metal powder or metal wire is injected directly into the melt pool, and the deposited metal then cools in a controlled and consistent pattern, creating a full metallurgical bond with the substrate with minimal to no dilution. This process is also referred to as Directed Energy Deposition (DED) process.
The primary application of this technology is in two areas:
- Enhancing the component life – by hardfacing or corrosion resistant material deposition
- Repair and Remanufacturing components to extend the life of component
Our low-heat process enables the deposition of coatings with unique properties such as high hardness, high toughness, wear resistance, and corrosion resistance on a variety of substrates causing minimal impact to metallurgical integrity of the substrate.
Synergy's laser cladding service offers ultra-low dilution with the base material and ensures excellent retention of coating material properties.
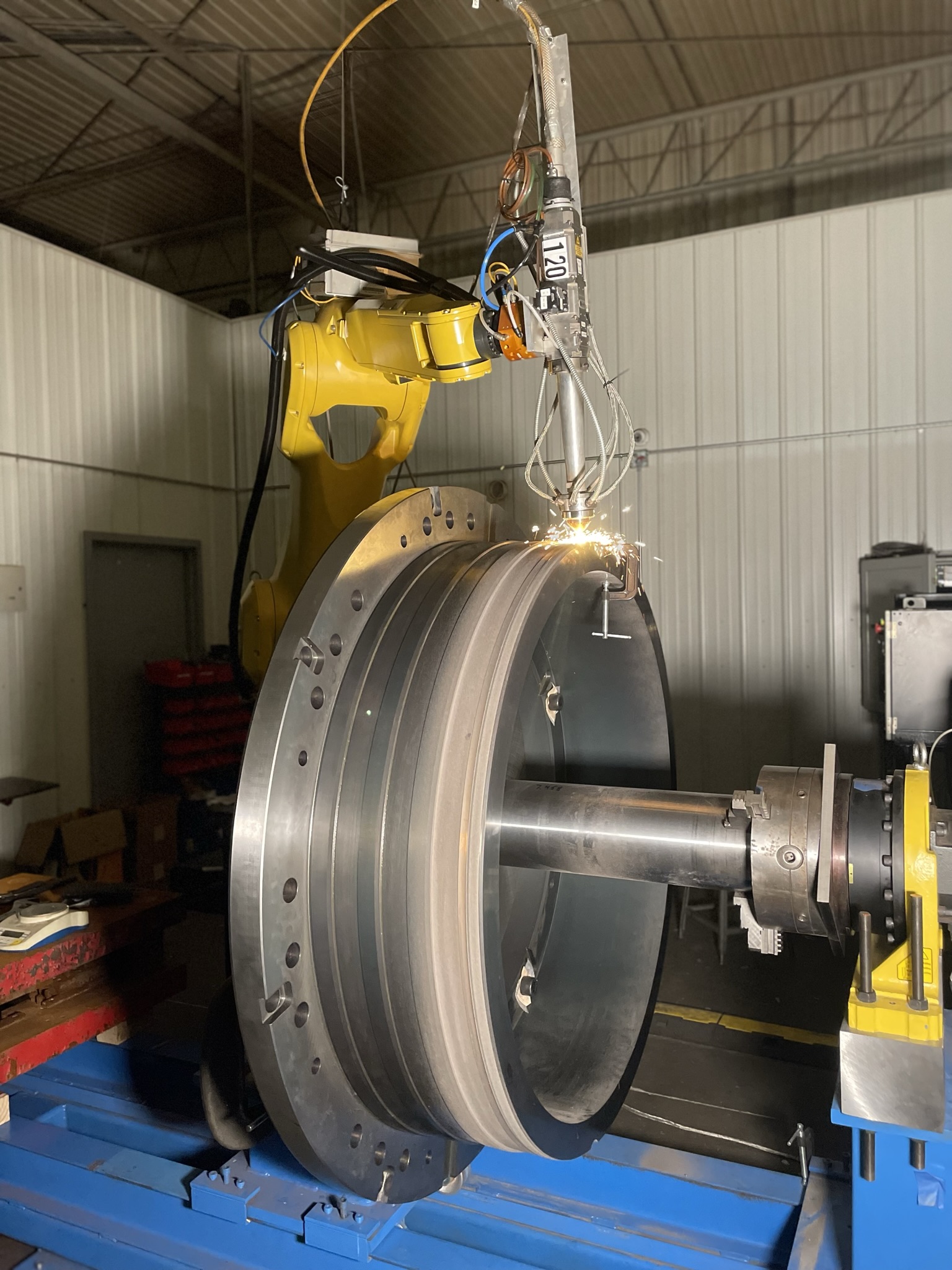
Advantages of Laser Cladding
Energy density of a Laser Cladding process is typically an order of magnitude higher than Arc based overlay processes such as Tungsten Inert Gas (TIG) or Plasma Transfer Arc (PTA). This translates to having a lowest heat input to deposit a desired volume of metal compared to any other weld overlay process. With the use of advanced pyrometers and process control, Synergy is able to consistently keep the heat input low while achieving highest quality and desired material properties. At Synergy , we offer comprehensive laser cladding services tailored to your specific needs. Our services include:
- Minimal to no distortion– for example, in critical components such as motor shafts, high precision shafts and spindles, bearing journals and other heavy rotating equipment, secondary processing such as straightening can be avoided when laser cladding is used. Heat sensitive applications such as motors, shafts can be rebuilt without damaging windings or motor components
- Minimal post machining – For applications such as oil and gas tools, marine drive shafts where post machining or grinding is required, laser cladding minimizes the grinding required saving cost in overall process.Typical grinding requirements are around 0.010"-0.030" per side.
- Minimal dilution – Dilution is typically defined by the amount of intermixing that happens between the base material and laser clad material. Typical laser clad deposits exhibit a dilution of less than 1% with base material compared to 10-15% dilution commonly seen in PTA and other arc welding processes. Due to minimal mixing with base material, a laser clad deposit typically results in material properties in 1 layer compared to multiple layers in arc process. This is a substantial savings in material costs.
- Little to no porosity (>99.9% density) – High-quality and dense coatings are produced which contain increased strength, hardness and wear resistance compared to partially dense coatings like welding or thermal sprays.
- No delamination or debonding – Laser Cladding is a superior alternative to thermal spray or chrome coatings. In applications such as hydraulic cylinders where substantial and bending loads are seen, laser clad layers do not delaminate, chip or crack resulting in prolonged life of the components when compared to hard chrome.
- Complex profiles – These can be laser clad and hard faced without the need to mask the surfaces. Hot stamping dies, Hot forging dies, High Pressure Die Casting (HPDC) tools and other complex components can be robotically programmed for repair. Synergy's proprietary ID Cladding technology enables laser cladding inside IDs as small as 1.5" (38.1 mm).
- Minimal Heat Affected Zone (HAZ) – Compared to conventional techniques such as PTA and other arc processes, Laser Cladding exhibits substantially lower HAZ. HAZ is hard region of material under the weld. A lower HAZ often indicates better performance under stress and fatigue loading.
What Laser Cladding Services Does Synergy Additive Offer?
Synergy Additive Manufacturing LLC, an ISO 9001:2015 certified company, offers top-tier, cost-competitive, high-quality Laser Cladding and High-Speed Laser Cladding services, ID cladding, and Machine Integration Services nationwide. Combined with grinding and pre-and post-machining capabilities, Synergy is a one-stop solution and is able to provide quick turnaround on your urgent repair needs.
capabilities include handling parts up to 5 feet in diameter, 15 feet in length, and weighing up to 14,000 pounds. Synergy specializes in internal diameter (ID) cladding for surfaces as small as 1.5 inches in diameter. The company works with a diverse array of materials, including nickel-based alloys like Inconel 625 and 718, iron-based and stainless steels such as 304 and 316 SS, cobalt-based alloys like Stellite 6 and 21, tungsten carbide blends, and aluminum alloys like AlSi10Mg.
These services are particularly beneficial for applications requiring minimal distortion, reduced post-machining, and strong metallurgical bonds without delamination or debonding. Industries include automotive, aerospace, marine, and oil and gas, where components demand enhanced wear and corrosion resistance.
Value Addition and Cost Competitiveness of Laser Cladding
Synergy Additive Manufacturing offers highly competitive pricing for its Laser Cladding services. The cost of laser cladding is influenced by several factors, including surface area, clad thickness, material type, and profile complexity. Over the past decade, advancements in laser technology have led to a significant decrease in the price of laser power sources while increasing their power output. Today, diode and laser power sources of up to 50kW are available, making laser cladding more cost-effective than ever.
In some applications, the cost per square inch of laser cladding is now comparable to traditional welding, PTA, and thermal spray technologies. The overall cost-effectiveness and added value of laser cladding depend on the specific application. The table below outlines common applications, key benefits, and cost savings associated with laser cladding, often achieved through reduced pre- and post-machining, minimal material usage, and enhanced product performance and durability.
Application/ Material | Value Addition and Cost Savings | Conventional methods | Advantages of Laser |
---|---|---|---|
Pump components/ Stellite TM 6, 12, 21, 17-4 PH, SS 431 | High | PTA/TIG | Minimal to no defects, material savings, minimal pre-post machining enhanced durability |
Hydraulic Cylinders/ Stellite TM , Inconel 625, 420 SS | High | Hard Chrome, Thermal Spray | No delamination, low HAZ, low coating failure, enhanced durability |
Steel Mill Rollers and Casters/ Tungsten Carbide | High | PTA/TIG | Improved high temperature performance, longivity |
High precision rotating equipment / SS 431, 420, 410 | High | Thermal Spray/ Hard Chrome | No delamination, low HAZ, enhanced durability |
Hot Stamping/Hot Forging Tools | High | PTA/TIG | Minimal HAZ, reduced hard milling, enhanced performance |
High Pressure Die Casting Tools/H13 | High- Moderate | TIG | Minimal post machining required, enhanced durability |
Press components and heavy duty shafts | High- Moderate | PTA/TIG | Minimum post machining, enhanced durability |
Tool and Die Repair/ Propritory alloy | Moderate | PTA/ TIG | Minimal post machining required, enhanced durability |
READ MORE ON LASER CLADDING HERE:
- Rockit 606 Hardfacing overlays for Mining and Agricultural Industries
- Laser Hardfacing with Tungsten Carbide
- Stellite 6 Overlay with Laser Cladding
- Electric Motor Shaft Repair using Laser Cladding
- Repair and Refurbishment of high precision shafts using Laser Cladding
- Laser Cladding vs. PTA and Thermal Spray
- Laser Cladding advantages over Hard Chrome for Dimensional Restoration